A. Eutectic steel, sub-eutectic steel, super-eutectic steel
1. Eutectic steel
Carbon dissolved in the lattice of iron to form a solid solution, carbon dissolved in α – iron solid solution called ferrite, dissolved in γ – iron solid solution called austenite. Ferrite and austenite both have good plasticity. When the carbon in the iron-carbon alloy can not be dissolved into the ferrite or austenite, the remaining out of the carbon will form a compound with iron – iron carbide (Fe 3C) The crystal organization of this compound is called carburite, which is extremely hard, plasticity is almost zero.
From the iron-carbon equilibrium state diagram, which reflects the relationship between the structure of steel and the carbon content of steel and the temperature of steel, it can be seen that when the carbon content is exactly equal to 0.77%, which corresponds to an alloy in which carburite (iron carbide) accounts for about 12% and ferrite for about 88%, the phase transformation of the alloy is achieved at constant temperature. That is, the carburized body and ferrite in this specific ratio, when the phase transformation occurs, if it disappears both disappear at the same time (when heated), and if it appears then both appear at the same time, in this point this organization is similar to the phase transformation of pure metals. For this reason, people treat this two-phase organization composed of a specific ratio as a kind of organization, and name it pearlite, and this kind of steel is called eutectic steel. That is, the steel with exactly 0.77% carbon content is called eutectic steel, and its organization is pearlite.
2. Sub-eutectoid steel
Most of the commonly used structural steels contain less than 0.5% carbon, because the carbon content is less than 0.77%, so the amount of carburite in the organization is less than 12%, so the ferrite will be partly removed to form pearlite with carburite, there will be excess, so the organization of this steel is ferrite + pearlite. The less the carbon content, the smaller the proportion of pearlite in the steel tissue, the lower the strength of the steel, but the better the plasticity, these steels are collectively called sub-eutectoid steel.
3. over-eutectoid steel
The carbon content of tool steel is often more than 0.77%, and the proportion of carburite in this kind of steel is more than 12%, so in addition to the formation of pearlite with ferrite, there is extra carburite, so the organization of this kind of steel is pearlite + carburite. This kind of steel is collectively called over-eutectoid steel.
B. Terms related to the mechanical properties of steel
1. yield point (σ s)
Steel or specimen in tension, when the stress exceeds the elastic limit, even if the stress no longer increases, and the steel or specimen still continues to undergo significant plastic deformation, called the phenomenon of yield, and the minimum stress value when the yield phenomenon is the yield point. Set Ps for the yield point s at the external force, Fo for the sample area, the yield point σ s = Ps/Fo (MPa), MPa is called MPa equal to N (Newton) / mm2, (MPa = 106Pa, Pa: Pascal = N/m2 )
2. yield strength (σ 0.2)
The yield point of some metallic materials is extremely inconspicuous and difficult to measure, so in order to measure the yielding characteristics of the material, the provision of permanent residual plastic deformation equal to a certain value (generally 0.2% of the original length) when the stress, known as the conditional yield strength or simply yield strength σ 0.2.
3. tensile strength (σ b)
The maximum stress value reached during the tensile process, from the beginning to the time of fracture. It indicates the size of the steel’s ability to resist fracture. The corresponding tensile strength and compressive strength, bending strength, etc.
Let Pb be the maximum tensile force reached before the material is pulled, Fo is the cross-sectional area of the sample, the tensile strength σ b = Pb/Fo (MPa). 4.
4 elongation (δ s)
After the material is pulled, the plastic elongation of the length of the original sample length of the percentage called elongation or elongation.
5. yield strength ratio (σ s / σ b )
The yield point of steel (yield strength) and the ratio of tensile strength, called the yield strength ratio. The greater the yield strength ratio, the higher the reliability of structural parts, generally 0.6-0.65 for carbon steel, 0.65-0.75 for low-alloy structural steel, 0.84-0.86 for alloy structural steel.
6. hardness
Hardness indicates the ability of a material to resist the pressure of hard objects into its surface. It is one of the important performance indicators of metal materials. Generally the higher the hardness, the better the wear resistance. Commonly used hardness indicators are Brinell hardness, Rockwell hardness and Vickers hardness.
(1) Brinell hardness (HB)
With a certain load (generally 3000kg) to a certain size (diameter is generally 10mm) of hardened steel ball pressed into the surface of the material, hold for a period of time, to load, the ratio of the load and its indentation area, that is, the Brinell hardness value (HB), the unit for the kilogram force / mm2 (N / mm2).
(2) Rockwell hardness (HR)
When HB>450 or the specimen is too small, the Brinell hardness test can not be used and Rockwell hardness measurement is used instead. It is a diamond cone with a top angle of 120 ° or a steel ball with a diameter of 1.59, 3.18 mm, pressed into the surface of the material under a certain load, and the depth of the indentation to find out the hardness of the material. Depending on the hardness of the test material, there are three different scales to express.
HRA: is the hardness obtained by using a 60kg load and a diamond cone indenter, and is used for extremely hard materials (e.g. carbide).
HRB: is the hardness obtained with a 100 kg load and a 1.58 mm diameter hardened steel ball, and is used for materials of lower hardness (e.g. annealed steel, cast iron, etc.).
HRC: is the hardness obtained by using 150kg load and diamond cone indenter, used for very hard materials (such as hardened steel, etc.).
(3) Vickers hardness (HV)
The Vickers hardness (HV) is obtained by dividing the surface area of the indentation by the load value with a load of 120 kg or less and a diamond square cone indenter with a top angle of 136° into the surface of the material.
Introduction To Steel Terminology
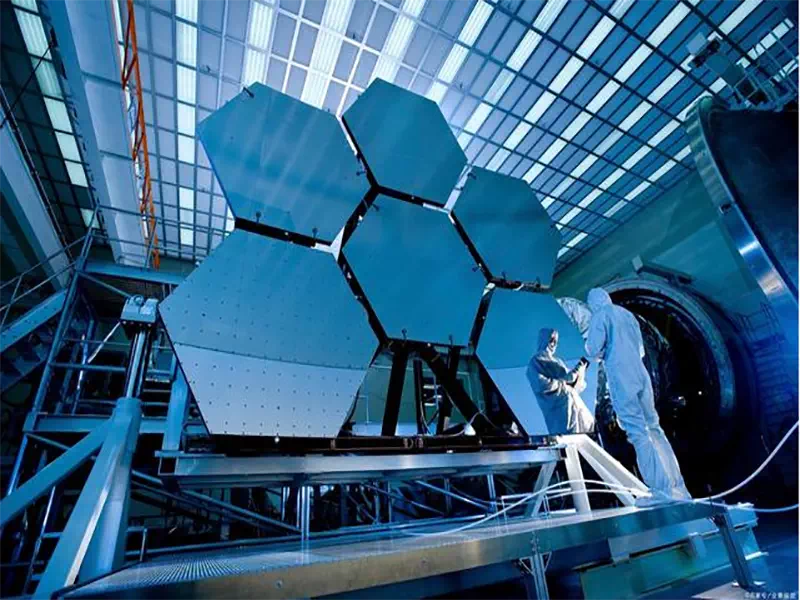
C. Terminology related to heat treatment of steel
1. annealing of steel
To heat steel to a certain temperature and hold it for a certain period of time, and then make it slowly cool, is called annealing. Annealing of steel is a heat treatment method in which the steel is heated to the temperature at which the phase change or partial phase change occurs, and then slowly cooled after holding. The purpose of annealing is to eliminate organizational defects, improve the organization so that the composition of uniformity and refinement of grain, improve the mechanical properties of steel, reduce residual stress; at the same time can reduce hardness, improve plasticity and toughness, improve cutting performance. So annealing is not only to eliminate and improve the organization defects and internal stresses left by the previous process, but also to prepare for the subsequent process, so annealing is a semi-finished product heat treatment, also known as pre-heat treatment.
2. Normalizing of steel
Normalizing is to heat the steel above the critical temperature, so that all the steel is transformed into uniform austenite, and then the heat treatment method of natural cooling in the air. It can eliminate over-eutectoid steel mesh carburizing body, for sub-eutectoid steel normalizing can refine the lattice, improve the overall mechanical properties, the requirements of the parts are not high with normalizing instead of annealing process is more economical.
3. Quenching of steel
Quenching is the steel heated to above the critical temperature, holding for a period of time, and then quickly put into the quenching agent, so that its temperature is suddenly reduced to a rate greater than the critical cooling rate of rapid cooling, and obtain a martensite-based unbalanced organization of the heat treatment method. Quenching can increase the strength and hardness of steel, but to reduce its plasticity. The quenching agents commonly used in quenching are: water, oil, alkaline water and salt solutions.
4. Tempering of steel
The steel has been quenched and reheated to a certain temperature, and then cooled by a certain method called tempering. Its purpose is to eliminate the internal stresses generated by quenching, reduce hardness and brittleness, in order to obtain the desired mechanical properties. Tempering is divided into high-temperature tempering, tempering and low-temperature tempering three types. Tempering is mostly used in conjunction with quenching and normalizing.
(1) tempering treatment: quenching and tempering after high-temperature heat treatment method called tempering treatment. High-temperature tempering refers to tempering between 500 -650 ℃. Tempering can make the performance of steel, the material is adjusted to a large extent, its strength, plasticity and toughness are better, with good overall mechanical properties.
(2) aging treatment: in order to eliminate precision gauges or molds, parts in long-term use, size and shape changes, often in the low-temperature tempering (low-temperature tempering temperature 150 -250 ℃) before finishing, the workpiece is reheated to 100 -150 ℃, hold 5-20 hours, this treatment for the quality of stable precision parts, known as aging. Ageing treatment of steel components at low temperatures or dynamic load conditions to eliminate residual stresses and stabilize the steel organization and dimensions is particularly important.
5. Surface heat treatment of steel
(1) surface quenching: is the surface of the steel parts by rapid heating to above the critical temperature, but the heat has not yet had time to transfer to the heart before rapid cooling, so that the surface layer is quenched in martensitic organization, while the heart does not undergo phase transformation, which achieves the purpose of surface hardening while the heart remains unchanged. Applicable to medium carbon steel.
(2) Chemical heat treatment: refers to the atoms of chemical elements, with the ability of atomic diffusion at high temperatures, it infiltrates into the surface layer of the workpiece to change the chemical composition and structure of the surface layer of the workpiece, so as to achieve the surface layer of steel with specific requirements of the organization and performance of a heat treatment process. According to the different types of infiltrated elements, chemical heat treatment can be divided into four kinds of carburizing, nitriding, cyanidation and metalizing method.
Carburizing: Carburizing is the process of infiltrating carbon atoms into the surface layer of steel. It also makes the workpiece of low carbon steel have the surface layer of high carbon steel, and then after quenching and low temperature tempering, the surface layer of the workpiece has high hardness and wear resistance, while the central part of the workpiece still maintains the toughness and plasticity of low carbon steel.
Nitriding: Also known as nitriding, is the process of infiltrating nitrogen atoms into the surface layer of steel. Its purpose is to improve the hardness and wear resistance of the surface layer, as well as to improve fatigue strength, corrosion resistance, etc.. At present, the production of gas nitriding method is mostly used.
Cyanidation: also known as carbonitriding, is the process of infiltrating carbon and nitrogen atoms into the steel at the same time. It makes the steel surface with the characteristics of carburizing and nitriding.
Metal infiltration: It is the process of infiltrating the surface layer of steel with metal atoms. It is to make the surface layer of steel alloyed, so that the surface of the workpiece has certain characteristics of alloy steel, special steel, such as heat resistance, wear resistance, oxidation resistance, corrosion resistance, etc.. Commonly used in production are aluminizing, chromium infiltration, boron infiltration, silicon infiltration, etc.
D. Explanation of the nomenclature of steel
" Medium plate "
Steel plate is a flat steel with a large width to thickness ratio and surface area. According to the thickness of the thin steel plate ( thickness <= 4 mm ) and thick steel plate ( thickness > 4 mm ) in practice, often <= 20 mm thick steel plate is called medium plate, thickness > 20 -60 mm plate is called thick plate, thickness > 60 mm plate is called extra thick plate, collectively referred to as thick steel plate. Steel plates with relatively small widths and long lengths, called steel strip, are classified as a separate species. Steel plate has great covering and accommodating capacity, and can be used as roofing panels, thatching materials and manufacturing containers, oil storage tanks, packaging boxes, train boxes, automobile shells, industrial furnace shells, etc.: can be cut and combined according to the requirements of use, made into a variety of structural and mechanical parts, but also into welded steel, to further expand the use of steel plate; can be bent and pressed into shape, made into boilers, containers, punching Automobile shells, civilian utensils, appliances, can also be used as welded steel pipes, cold-formed steel billets. As a result of the above characteristics, more than 50% of the total steel production. China to meet the needs of large-scale capital construction, industrial products and high-grade consumer goods in the past, the demand for steel plate has increased sharply. In order to meet the needs of the new situation, the production of steel plates in China has also developed greatly over the years, and a number of advanced steel plate production backbone enterprises such as Wuhan Iron and Steel have been built. Steel plates are supplied in sheets or rolls. The specification of sheet steel is expressed in mm of thickness * width * length. It is very important to be familiar with the specifications of plates and strips and to make full use of them in width and length to improve material utilization, reduce inappropriate margins, reduce man-hours and product costs. In the purchase of plate, strip material, should try to use for the product blank whole times the specifications. If it belongs to the definite product, choose the plate and strip material close to the definite size, you can order the reasonable material of the definite size or times the size, and implement the method of material under the set, which can significantly improve the utilization rate of the plate and strip material. The multiple use of edge residues between enterprises and enterprises, and between industries and industries is also an effective way to improve material utilization and save material by practice.
" Rebar "
Rebar for reinforced concrete is a straight or coiled steel for reinforcement of reinforced concrete, its shape is divided into two types of light round bars and deformed bars, the delivery status of straight bars and coils. Light round bars are actually small round bars and discs of ordinary low carbon steel. Deformed bars are bars with ribs on the surface, usually with 2 longitudinal ribs and evenly distributed horizontal ribs along the length direction. The shape of the cross-rib is spiral, herringbone, crescent-shaped 3 kinds. The nominal diameter is expressed in millimeters. The nominal diameter of a deformed bar is equal to the nominal diameter of a light round bar of equal cross-section. The nominal diameter of reinforcing bars is 8 – 50 mm, the recommended diameters are 8, 12, 16, 20, 25, 32, 40 mm. Reinforcing bars are mainly subjected to tensile stresses in the concrete. The deformed reinforcement has a greater bonding capacity with the concrete due to the ribs, and is therefore better able to withstand the effects of external forces. Reinforcing bars are widely used in various building structures, especially in large, heavy, light thin-walled and high-rise structures.
"I-beam"
I-beams, also known as steel beams, are long steel bars with an I-shaped cross section. Its specification is expressed in millimeters of waist height (h) * leg width (b) * waist thickness (d), such as “I 160*88*6”, which means I-beam with waist height of 160 mm, leg width of 88 mm and waist thickness of 6 mm. The specification of I-beam can also be expressed by model number, which indicates the number of centimeters of waist height, such as I 16#. If there are several different leg widths and waist thicknesses of I-beams with the same waist height, they should be distinguished by adding a b c to the right of the model number, such as 32a # 32b # 32c # etc. I-beam is divided into ordinary I-beam and light I-beam, and the specification of hot-rolled ordinary I-beam is 10-63#. The specifications of hot-rolled ordinary I-beams are 12-55#, which are supplied by agreement between supply and demand. I-beams are widely used in various building structures, bridges, vehicles, brackets, machinery, etc.
"Channel Steel"
Channel steel is a long steel bar with a grooved cross section. Its specification, such as 120*53*5, indicates that the waist height is 120 mm, the leg width is 53 mm channel, the waist thickness is 5 mm channel, or 12# channel. If there are several different leg widths and waist thicknesses of the same channel with the same waist height, they should be distinguished by adding a b c to the right of the model number, such as 25a # 25b # 25c # etc. The channel steel is divided into ordinary channel steel and light channel steel. The specifications of hot-rolled common channel are 5-40#. Hot-rolled steel channels of 6.5-30# are supplied by mutual agreement between supply and demand. Channels are mainly used in building structures, vehicle construction and other industrial structures, and are often used in combination with I-beams.
" Patterned Plate "
Patterned steel plate, also known as webbed steel plate, is a steel plate with a diamond-shaped or protruding edge on its surface. Because of its surface protrusions, patterned steel plate has an anti-slip effect and can be used as flooring, factory escalators, work shelf treads, ship decks, automobile flooring, etc. The specification of patterned steel plate is expressed by the basic thickness (the thickness of the protrusions is not counted), and there are 10 kinds of specifications from 2.5 to 8 mm. The patterned steel plate is rolled with No.1-3 class B ordinary carbon structural steel, and the chemical composition is in accordance with the provisions of GB700 “Technical Conditions for Ordinary Carbon Structural Steel”.
E. Steel types
1. low carbon steel – also known as soft steel, carbon content from 0.10% to 0.30% low carbon steel is easy to accept a variety of processing such as forging, welding and cutting, commonly used in the manufacture of chains, rivets, bolts, shafts, etc..
2. medium carbon steel – carbon content from 0.30% to 0.60%
3. high carbon steel – often called tool steel, carbon content from 0.60% to 1.70%, can be hardened and tempered. Hammers, crowbars, etc. are made of steel with 0.75% carbon content; cutting tools such as drills, taps, reamers, etc. are made of steel with 0.90% to 1.00% carbon content.
4. alloy steel – steel with other metals such as chromium, nickel, tungsten, vanadium, etc., to give some new characteristics. Due to the incorporation of various alloying elements, alloy steels can have different properties such as corrosion resistance, heat resistance, abrasion resistance, shock resistance and fatigue resistance.
5. high-speed steel – contains a variety of components and amounts, such as tungsten, chromium, vanadium, cobalt and molybdenum. Cutting tools made of high speed steel can cut hard materials at high speeds and can take strong cuts. High-speed steel cutting tools can maintain sharp edges at high speeds, while other steels may become dull.