The application of fastener products has been throughout the machinery manufacturing, the production of galvanized hook mesh, electronics, precision instruments, chemical industry, transportation, aerospace, etc., which has great significance in the national economy.
Comparison of galvanizing and hot-dip galvanizing
galvanizing
1. Principle
Because zinc is not easy to change in dry air, and in humid air, the surface can form a very dense zinc carbonate film, this film can effectively protect the interior from corrosion. And when the coating is damaged for some reason and the substrate is not too large, the zinc and steel substrate form a microbattery, so that the fastener substrate becomes the cathode and is protected. It is widely used in automobile transportation and other industries, but what is needed is trivalent chromium passivation layer and zinc-nickel alloy plating closed coating to reduce the harmful and toxic layer of hexavalent chromium passivation.
2. Performance characteristics
Zinc coating is thick, the crystallization is fine, uniform and no porosity, good corrosion resistance; The zinc layer obtained by electroplating is pure, corroded slowly in acid, alkali and other fog, can effectively protect the sand fixing parts matrix, galvanized layer after chromic acid passivation form white, color, military green, beautiful, has a certain decorative, because of the good ductility of galvanized layer, so it can be cold stamping, rolling, bending and other forming without damaging the coating.
3. Application scope
The fields involved in electric galvanizing are more and more extensive. The application of fastener products has been throughout the machinery manufacturing, the production of galvanized hook mesh, electronics, precision instruments, chemical industry, transportation, aerospace, etc., which has great significance in the national economy.
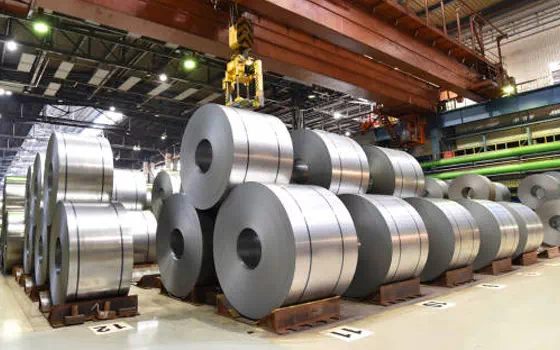
Hot-dip galvanizing
1. Principle
The hot dip zinc layer is formed in three steps in the liquid state of zinc. The iron base surface is dissolved by zinc liquid to form zinc and iron alloy layer. The zinc ions in the alloy layer further diffused to the matrix to form the zinc and iron miscible layer. The alloy layer is coated with zinc.
2. Performance characteristics
A thick and dense pure zinc layer covering the surface of the steel fastener can avoid the contact between the steel matrix and any corrosive solution and protect the steel fastener matrix from corrosion. In the general atmosphere, the zinc layer forms a very thin and dense zinc oxide layer. It is difficult to dissolve in water, so it plays a certain role in protecting the steel fastener base. If zinc oxide and other components in the atmosphere to form insoluble zinc salt, the anti-corrosion effect is more ideal; With zinc-iron alloy alloy layer, compact, in Marine salt spray atmosphere and industrial atmosphere performance unique corrosion resistance; Due to the firm combination, zinc-iron miscible, with strong wear resistance; Because zinc has good ductility, its alloy layer is firmly attached to the steel matrix, so hot dip galvanizing can be cold stamping, rolling, drawing, bending and other forming processes, without damaging the coating; The hot zinc dipping of steel structural parts is equivalent to a single annealing treatment, which can effectively improve the mechanical properties of the steel matrix, eliminate the stress during the forming and welding of steel parts, and is conducive to the turning of steel structural parts. The fastener surface after hot dipping zinc is bright and beautiful. Pure zinc layer is the most plastic layer of hot dip zinc, its properties are basically close to pure zinc, has good ductility.
3. Application scope
This plating method is especially suitable for all kinds of strong acid, alkali mist and other strong corrosion environment.