Vale has launched a new green briquette product that can help steel mills reduce greenhouse gas emissions by about 10 percent in the production process.
The green briquettes are made from iron ore and treated iron-bearing sand ore, which is known to reduce greenhouse gas emissions by avoiding hot bursts during blast furnace heating and reducing steel mills’ reliance on the sintering process. This green briquette product uses a cold-pressing process and consumes less energy. The product also reduces emissions of particulate matter, sulfur dioxide, and nitrogen oxides, and requires no water in the production process.
The launch of the green briquettes is in line with Vale’s strategic goal to reduce Scope 3 (indirect emissions from product value chain activities) CO2 emissions by 15% from 2018 levels by 2035. In absolute terms, this means that the company will need to reduce its CO2 emissions by at least 90 million tons by 2035.
”The Green Briquettes product is one of the revolutionary iron ore products introduced by Vale. until the 1960s, Vale’s base product was a high iron content lump ore. Since then, as lump ore mining declined, we built our first pellet ore plant in Brazil, enabling the use of pellet concentrate. Today, we are launching a green briquette product that will revolutionize the steel production process.” Marcello Spinelli, executive vice president of Vale’s iron ore business, said.
The green briquettes will be produced first at pellet plants 1 and 2 in the Tubaräo integrated operation in Vitoria, Espírito Santo, Brazil, and at the Vargem Grande integrated operation in Minas Gerais. The Tubaräo 1 and 2 pellet plants are being renovated for this purpose, while a new plant is being built at the Vargem Grande complex. It is understood that these three plants will have an initial capacity of about 7 million tons per year and are expected to be operational in 2023, with a total investment of US$185 million. In the long run, Vale expects to produce more than 50 million tons of green briquettes per year in the future and plans to reduce CO2 emissions by about 6 million tons per year.
According to the report, Vale’s new green briquettes were developed in 2004 by researchers at the then Vale Ferrous Technologies division in Victoria, and in 2008 the division was integrated into the Center for Technology in Ferrous (CTF) in Nova Lima, Minas Gerais, a center of excellence for developing products that improve industrial productivity for Vale’s customers.
Early industrial testing of this green briquette product takes place in 2019 in a wood charcoal blast furnace, with large-scale coke blast furnace testing beginning in 2020. “The test results are satisfactory and we believe we are ready to start building the first plants and bringing the product to market.” Rogerio Nogueira, director of Vale’s iron ore marketing department, said.
Vale has been working with customers to develop carbon reduction roadmaps and discuss partnerships in the decarbonization sector since announcing its Scope 3 carbon reduction target and signed a memorandum of understanding with Ternium on August 19. According to this MOU, both parties agreed to conduct an economic feasibility study on a potential investment opportunity to build a green briquette products plant within Ternium’s Brazil plant.
Also (Reporter Zhu Xiaobo) Recently, Vale officially launched self-driving trucks at the Caracas integrated mine. To date, Vale has commissioned six self-driving trucks and four automated drilling rigs at its Caracas iron ore complex in Pará State, Brazil. The company plans to increase the number of self-driving trucks in use at the site to 10 and the number of automated rigs to seven by the end of this year.
It is understood that the self-driving trucks used at the Caracas integrated mine can carry 320 tons of iron ore in a single trip. 2019, the company has dedicated an area in Caracas to test the performance of self-driving trucks. At the end of August this year, the company completed the last test of self-driving trucks and officially opened them on September 1.
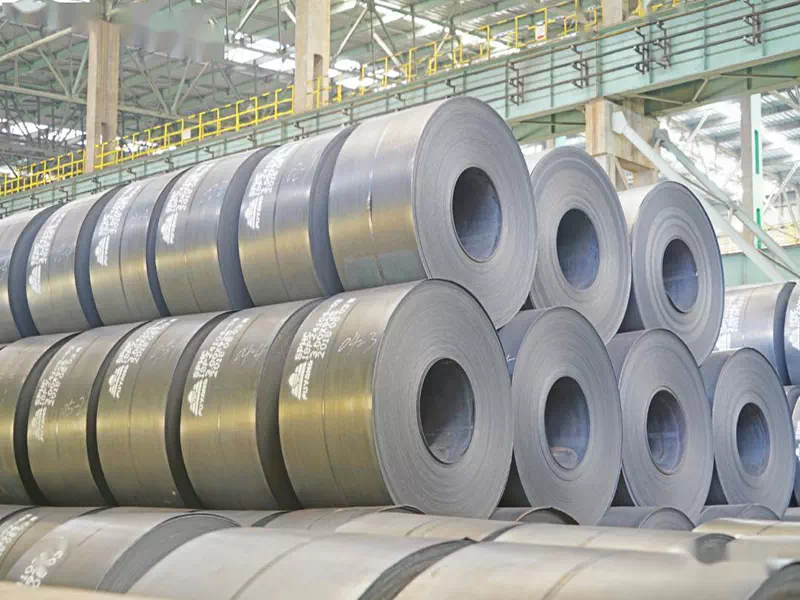
Translated with www.DeepL.com/Translator (free version)
Vale Launches Green Briquettes That Could Reduce Greenhouse Gas Emissions By About 10 Percent For Steel Mills
In 2016, Vale began automated operations at its Brucuto mine in Minas Gerais, Brazil. Today, the number of self-driving trucks operating at the Brucuto mine is 13. Since the start of the program, there has never been a safety incident at the Brucuto mine due to an uncontrolled self-driving truck. As the self-driving trucks’ performance continues to stabilize and their average speed continues to accelerate, fuel consumption will be reduced by about 5% and CO2 and particulate emissions will be reduced as well. According to the relevant data, self-driving technology is expected to extend the service life of trucks by about 7% and the service life of tires by about 25%.
According to the report, self-driving trucks are equipped with computer systems, global positioning systems, radar and artificial intelligence control system, and can automatically travel between the mining area and the unloading area and efficiently start work. Once a risk is detected, the self-driving truck immediately stops until the road is cleared of obstacles. The self-driving truck’s safety system is equipped with sensors that detect large objects, such as large rocks, other trucks and workers around the road, effectively avoiding rollovers and collisions.
”The commissioning of self-driving trucks at the Caracas integrated mine is another major step towards Vale’s goal of becoming a safety benchmark for the mining industry and achieving a 33% reduction in CO2 emissions by 2030.” Antônio Padovezi, director of Vale’s Northern Corridor branch, said, “Self-driving technology reduces the probability of risk for employees operating in the mine, while delivering significant environmental benefits.”
The implementation of Vale’s automation program has been expanding since the beginning of this year, with a total investment of approximately $34 million planned for the full year 2021. By the end of this year, Vale plans to deploy 23 self-driving trucks, 21 automated drilling rigs and four automated stacker and reclaimer yards in four Brazilian states of Pará, Minas Gerais, Maranhão and Rio de Janeiro within its operating areas. In addition, Vale has automated operations in many of its operating areas outside Brazil, deploying automated rigs and automated buckets in its Canadian operations and automated stacker and reclaimer yards in its Malaysian operations.
The self-driving trucks do not have operators in the cockpit, but the mines still require employees to operate some of the equipment. Vale said equipment such as graders and tractors operating in the mines will continue to be operated by human drivers. The company is actively training equipment operators to help them learn how to work with self-driving trucks. To date, the company has trained 32 operators and plans to complete training for 120 operators by the end of this year, for 208 hours of training per operator and nearly 25,000 cumulative hours of training.
”Automating operations always puts employees at the center of decision-making.” Pedro Bemfica, Vale’s automation project manager, said, “The introduction of digital technology drives employees to develop professional skills and helps them prepare for the digital transformation of the mining industry.”
Translated with www.DeepL.com/Translator (free version)