PPGI is a product based on a hot-dip galvanized plate and a hot-dip aluminum-zinc plate. After surface pretreatment (chemical degreasing and chemical conversion treatment), one or more layers of organic coatings are coated on the surface and then baked and cured. It is also namedPPGIbecause it is coated with organic coatings of different colors
In addition to the protection of the zinc layer, the organic coating on the zinc layer has the function of covering and protecting to prevent the steel strip from rusting, and its service life is about 1.5 times longer than that of the galvanized strip.
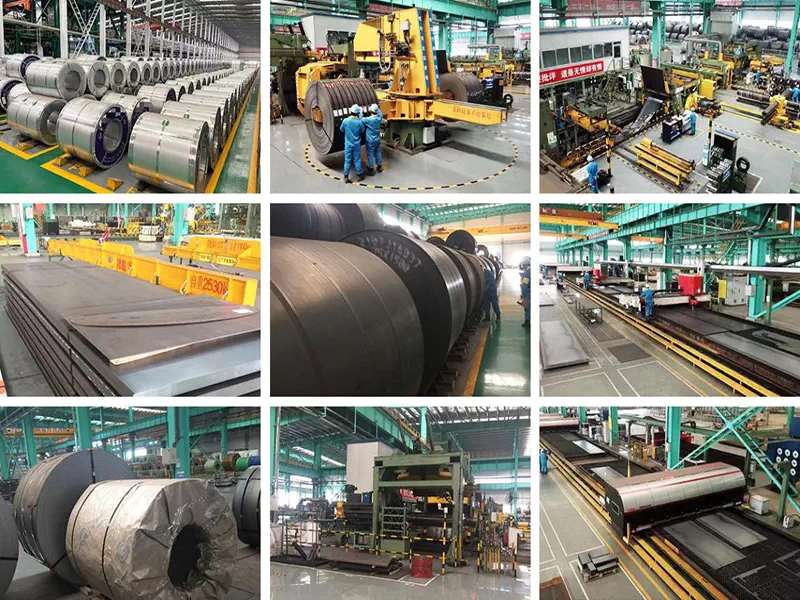
Knowledge of PPGI
PPGI application:
It has lightweight, has a beautiful appearance, and has good anti-corrosion performance, and can be directly processed, mainly used in advertising, construction, household appliances, electrical appliances, furniture, and transportation industries.
According to the different environments, we choose suitable resin, such as polyester silicon modified polyester, polyvinyl chloride plastic Sol, polyvinylidene chloride. The user can choose according to the use
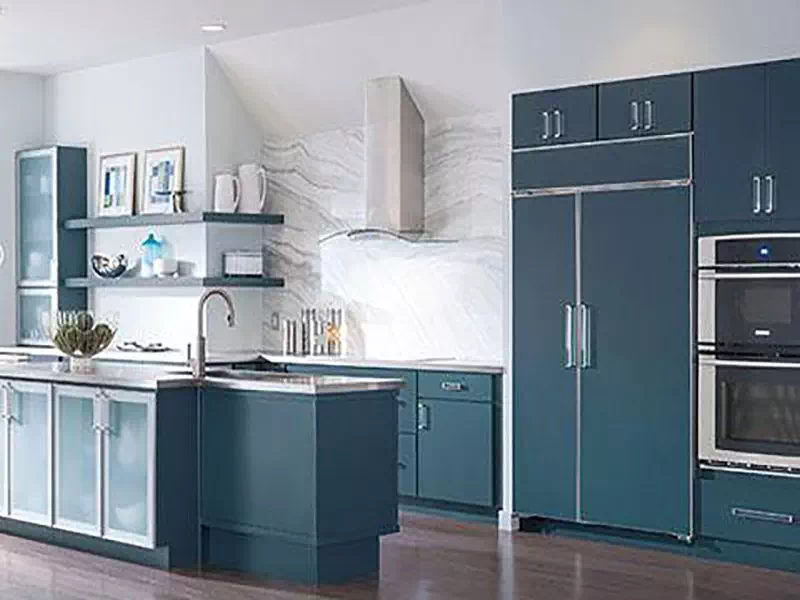
Knowledge of PPGI
Type of coating structure:
2/1:Twice on the top, once on the bottom, twice on the oven.
2/1M: The upper and lower surfaces are painted twice and baked once.
2/2:The upper and lower surfaces are painted twice and baked twice.
Use of different coating structures:
2/1:Single-layer back surface paint corrosion resistance, scratch resistance is poor, but has good adhesion, mainly used in the sandwich panel;
2/1M: Good corrosion resistance, scratch resistance, and processing molding, with good adhesion, suitable for single-layer profiled and sandwich panels.
2/2:The corrosion resistance, scratch resistance, and processing formability of double-layer back coating are good, most of them are used in single-layer press-type plates, but their poor adhesion, not suitable for a sandwich plate.
Classification of ppgisubstrate:
Hot Dip galvanizing substrate:
The product obtained by coating the organic coating on the hot-dip galvanized steel sheet is the hot-dip galvanized color-coated sheet. Hot-dip galvanized color coated sheet in addition to the role of zinc protection, the surface of the organic coating also plays the role of insulation protection, Rust Prevention, longer service life than hot-dip galvanized sheet. The zinc content of hot-dip galvanizing substrate is generally 180g/m2(double-sided), and the highest zinc content of hot-dip galvanizing substrate for building exterior is 275g/m2.
Hot Dip aluminized zinc substrate:
Hot Dip aluminized zinc steel (55% al-zn) is used as the new coating substrate, usually containing 150g/m2 (double side) of aluminized zinc. The corrosion resistance of the hot-dip galvanized sheet is 2 ~ 5 times as high as that of a hot-dip galvanized sheet. Continuous or intermittent use at temperatures up to 490 °C will not result in severe oxidation or scale formation. The ability to reflect heat and light is 2 times that of hot-dip galvanized steel sheet, and the reflectivity is more than 0.75 is the ideal building material to save energy.
Characteristics of PPGI substrate:
Hot-dip galvanized substrate: a sheet of steel is dipped into a molten zinc bath to form a zinc coating on the surface. The galvanized sheet has good adhesion and weldability.
Hot-dip aluminized zinc substrate: the product is 55% al-Foshan-zn plated, with excellent anti-corrosion properties, and its service life is more than four times that of ordinary galvanized steel. It’s a replacement for galvanized sheets.
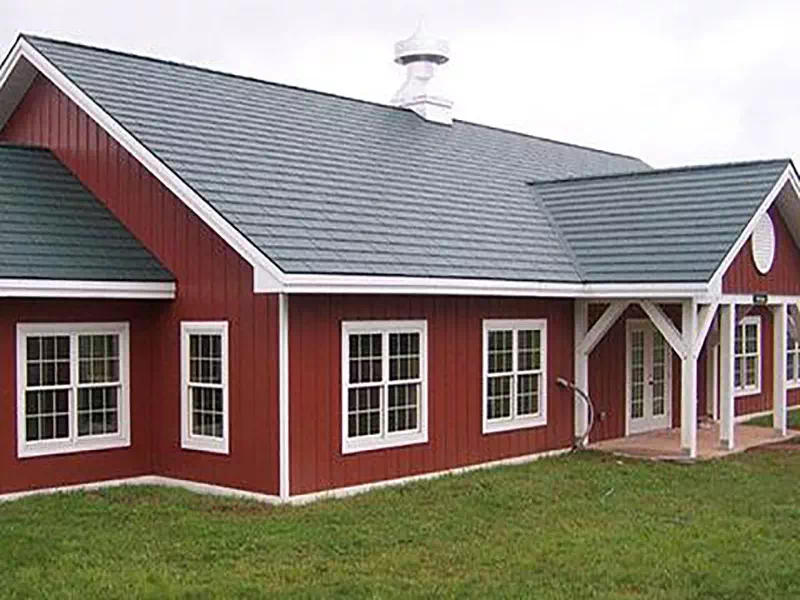
Knowledge of PPGI
Product characteristic:
(1)good durability, corrosion resistance, and longer life compared to galvanized steel;
(2) good heat resistance, and galvanized steel sheet compared to the more difficult to change color at high temperature;
(3)It has good thermal reflectivity
(4) it has similar machinability and spraying performance to galvanized steel sheet
(5)It has good welding performance.
With a good performance to price ratio, durable performance, and very competitive price. As a result, both architects, engineers, and manufacturers have been widely used in industrial buildings, steel structures, and civil facilities, such as garage doors, gutters, and roofs
PPGI coating:
1. Hot Dip galvanizing production process: cold rolled coil → uncoiler → coiler leveler → thickness gauge → double shear → automatic lap welding machine → pre-cleaning → inlet looper → continuous annealing furnace → jet electric induction heating ceramic zinc pot → gas knife → small zinc spangle or alloy furnace (reserved)→ cooling section after plating → coating thickness gauge → water quenching tank → dryer → skin pass → stretch straightening machine → chemical treatment (chromic acid passivation)→ dryer → outlet looper → electrostatic oiling → coiler。 The technological content in the process is the highest annealing and galvanizing two parts, so here to focus on annealing and galvanizing. Annealing is a metal heat treatment process in which the steel is heated to a predetermined temperature and then cooled slowly after a certain period.
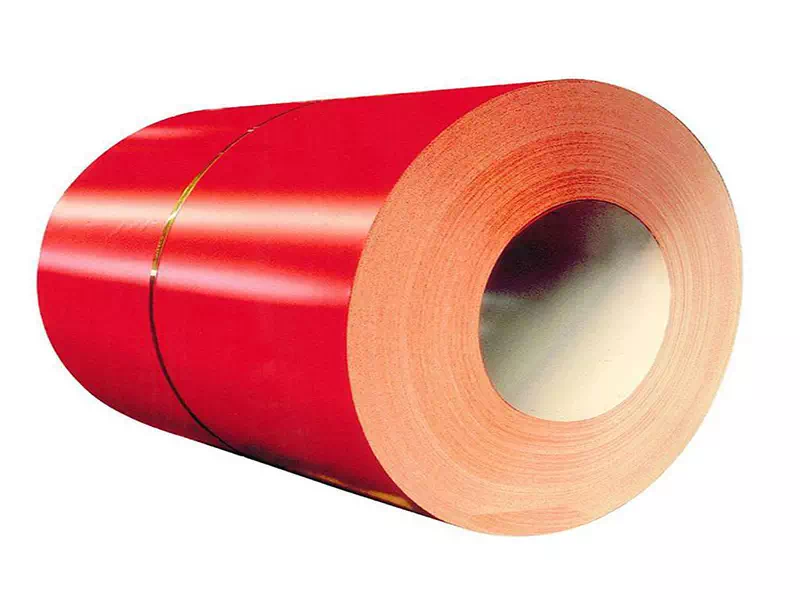
Knowledge of PPGI
The purpose of annealing:
(1) to improve or eliminate all kinds of structural defects and residual stresses in the process of casting, forging, cold rolling, and welding, and to prevent deformation and cracking.
(2) soften the workpiece for cutting.
(3) refine the grain and improve the structure to improve the mechanical properties of the workpiece.
HOT-DIP GALVANIZING:
At present, the hot-dip galvanizing production process mainly has the improved senjimir method, American steel joint method, Huilin method, and Silas method. Considering the investment, product quality, output, safety, energy-saving, and consumption reduction, the improved senjimir method is more advantageous, so it plays a leading role in the hot-dip galvanizing process.
The modified senior method uses non-oxidation heating, and the oxidation on the surface of the strip is very weak, so it is easy to reduce the oxide
In the improved senjimir process, the steel strip is first heated in an oxidation-free furnace with the temperature ranging from 1150 °C to 1250 °C, and then the oxide on the surface of the steel strip is quickly reduced in a reduction furnace with a protective atmosphere (N2 + H2) above 950 °C, the Reduced Steel Strip is put into a hot-dip pot in a sealed chamber with protective atmosphere. The temperature of hot-dip galvanizing is 680 ~ 750 °C. for hot-dip galvanizing, a special process is needed to control the temperature because the melting point of zinc is 420 °c and the vaporization temperature is 908 °C, the melting point of aluminum is 660 °c, the vaporization temperature is about 1200 °C, and the melting point of silicon is 1410 °C. The thickness and surface quality of the zinc coating is guaranteed by an air knife. After the hot-dip galvanizing steel strip comes out of the bath, the Strip is rapidly cooled to below 480 °C by controlled cooling. Finally, the Strip is cooled slowly into the passivation tank, and the coated steel sheet is passivated, a protective and decorative oxide film is formed, and then the strip is straightened online to improve its shape and mechanical properties. Finally, the Strip is taken up at the tail of the unit by various conveying equipment
The surface of the coating see table
Category Item Categories Code name
Type of coating Pure zinc coating Z
Zinc-iron alloy coating ZF
Coating form a,b Equal thickness coating A (g/m2)/B (g/m2 ) (A=B) A/B
Differential coating A (g/m2)/B (g/m2) (A≠B)
Surface texture Normal zinc Z
Smooth zinc G
Small zinc X
Smooth small zinc GX
Zero zinc N
Zinc-iron alloy R
Surface treatment Chromic acid passivation L
Oiled Y
Chromic acid passivation+Oiled LY
Coating of color coated sheet:
Color coiling production process:
Inlet End → uncoiler → pre-cleaning → inlet looper → cleaning → coater → chemical coater → drying oven → primary coater → drying oven → cooling → finishing oven → drying oven → cooling → export looper → shearer → coiler. In the above process, if the cleaning and degreasing process is not good, the adhesion between the primer and the galvanized sheet is not good.
In addition, in the production process of PPGI color difference is due to (1) paint itself caused by the color difference. (2) The chromatic aberration is caused by the drying oven process. (3) thickness of paint film.
The use of PPGI:
If the use of the page is not appropriate, the result is not a high standard of materials, resulting in waste, is the material performance can not meet the use of requirements, the use of the need to choose according to the use of the page.
1、The choice of substrate
(1) cold-rolled substrate: poor corrosion resistance, can be used to make home appliances parts
(2) galvanized substrate: Corrosion Resistance Than cold-rolled plate, generally for home appliances shell, furniture, interior decoration.
(3) hot-dip (aluminum) zinc substrate: corrosion resistance, external construction.
2、Coating Selection
(1) color: General Color for White Gray, sea blue, special color order to increase the price and order time.
(2) GLOSS: the Gloss of the film is high, medium, and low. General Construction for 30-70 something O low gloss color coated roll
(3) corrosion resistance.
3、The choice of coating technology general outer plate with 2/2 PPGI, field composite plate type can also use 2/1 PPGI, EPS composite plate must use 2/1 PPGI, to have better adhesion, the aluminized zinc plate is generally used for roofing site composite plate after some process can also be used aluminized zinc plate to do EPS composite plate.
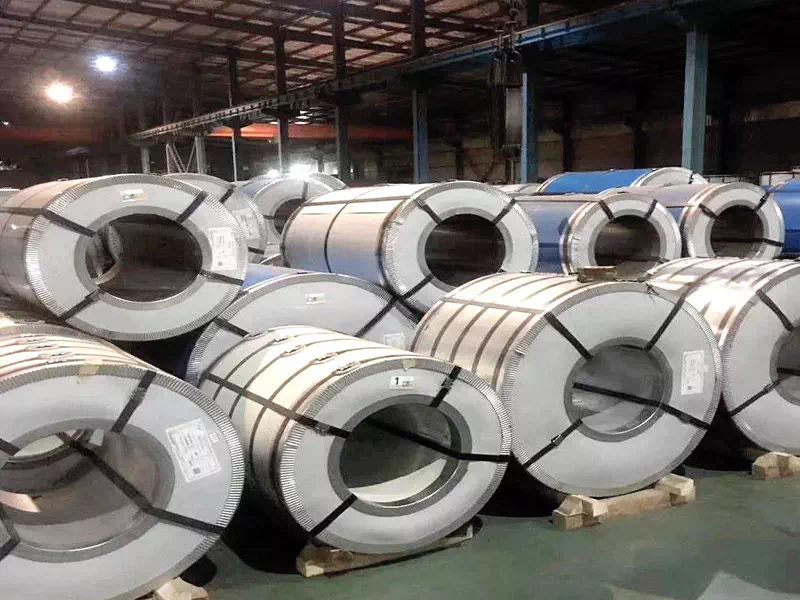
Global crude steel production up 4.8% in January
4、Attention in the use of the problem
(1) PPGI used in a building, the use of the same manufacturer the same production line at the same time products, to avoid mixing.
(2) the necessary peritoneum during pressing forming, such as PVDF coated color coated sheet, aluminized zinc-coated sheet.
(3) when the PPGI is sheared, the surface of the equipment in contact with the PPGI should be covered with a rubber mat.
(4) remove the metal chips in time to avoid scratching the coating on the surface of the PPGI.
(5) zinc can be used as a sacrificial anode to protect the steel, but when in use, try to place the incised part of the PPGI in the hidden part, there are strict requirements of the project to protect the incisions.
(6) after the installation of the project, the welding spots and metal chips leftover from the construction should be removed in time to avoid corrosion of the color plate